The Best Audiophile Cables You’ve Probably Never Heard Of
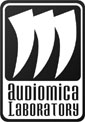
We first came across Audiomica from a review in 6Moons. The review really impressed us so we asked for some samples and they truly surprised us in their performance. In fact they sounded better than anything else we had ever heard and they rest is history. These cables really allowed our reference system to shine. No sweetening or smoothing off the higher frequencies, no artificial bass lift, all the leading edges in the right place at the right time, truly excellent stuff. Then the biggest surprise came when we found out the price, Audiomica’s top of the line cables were less expensive than our previous reference cables.
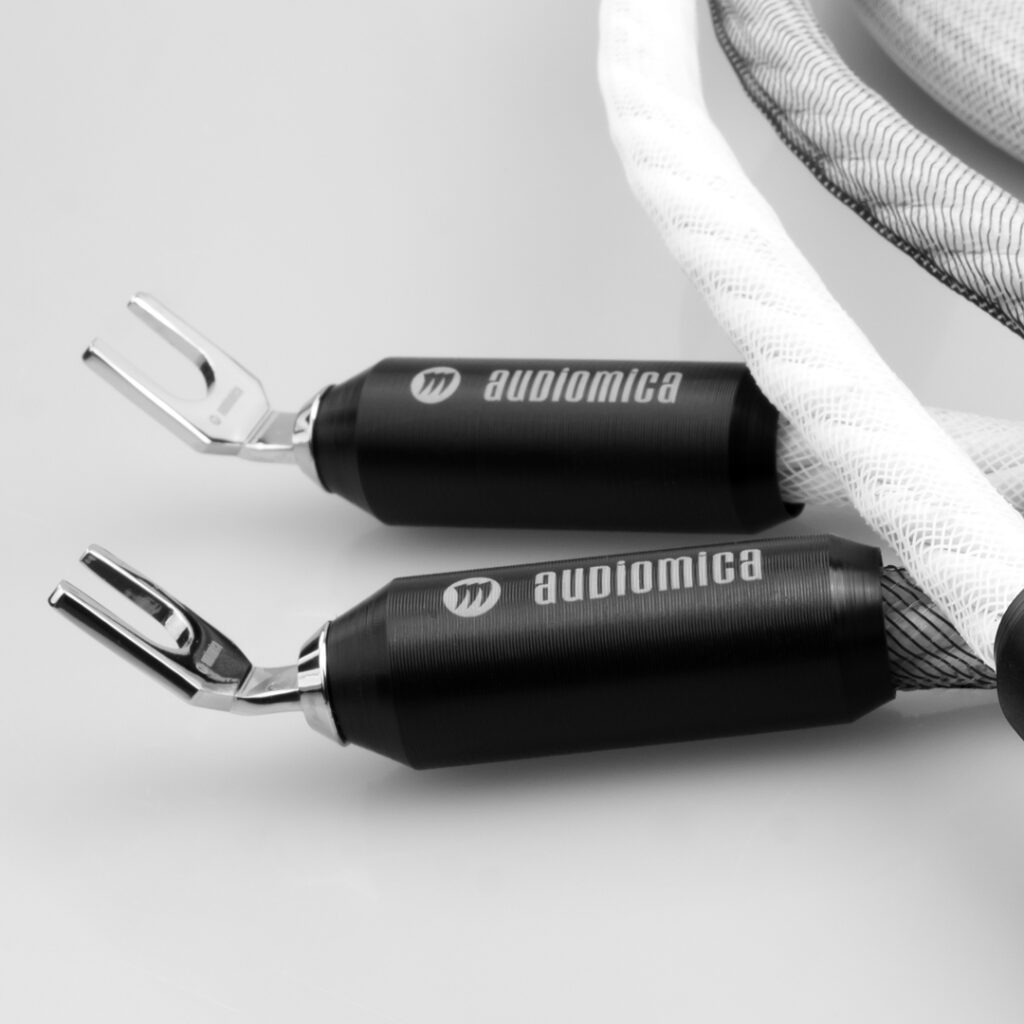
In addition to the many good cable companies, the HiFi cable and interconnect industry is full of performance claims and counter claims, hype, clever marketing and some would say smoke and mirrors. What struck us about the Audiomica cables is that they are plain musical and you forget about the equipment and want to just listen to music.
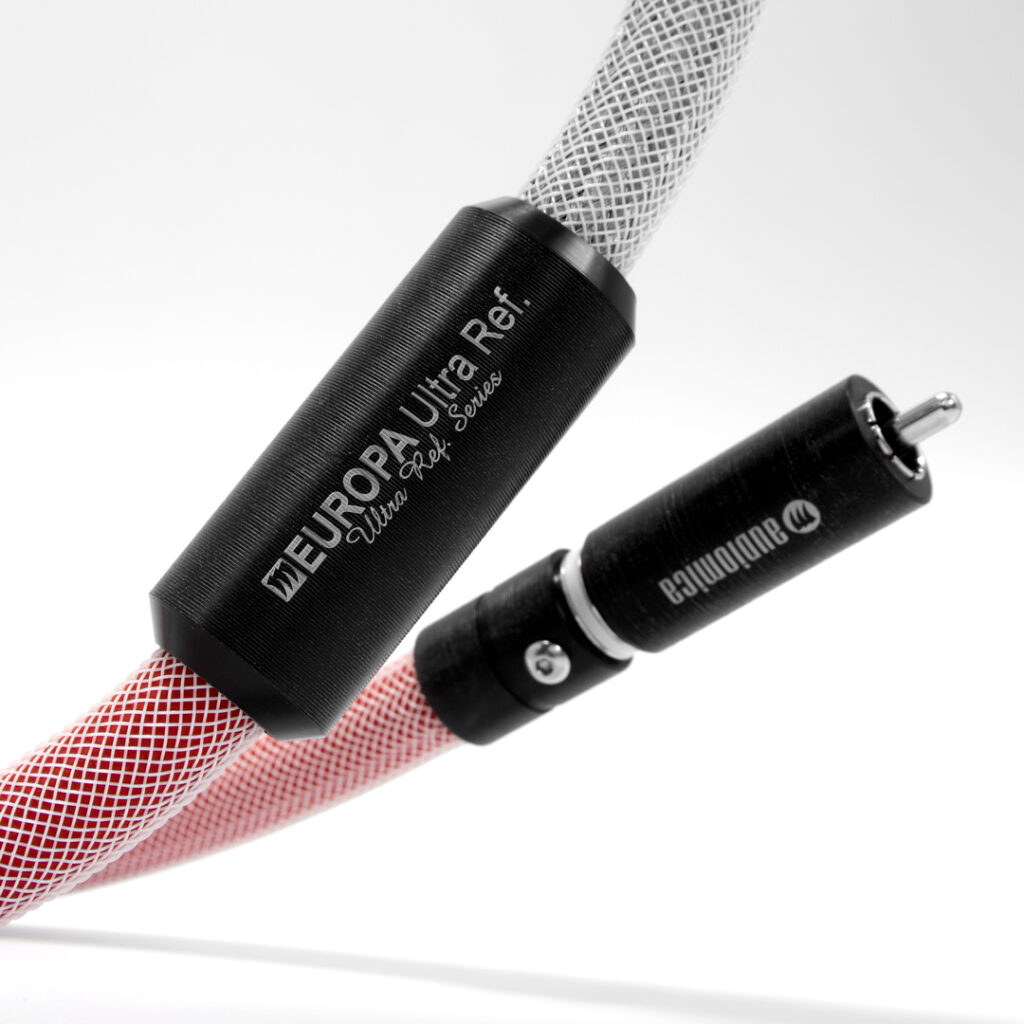
Audiomica Laboratory Introduction
Audiomica has been present in the audiophile market for more than twelve years, at first as hobbyists and now as a manufacturing and trading company. After the years of research, they found out that the quality of audio cables is not only affected by such obvious aspects as the kind of conductor, weave, screen and the composition of raw material but also by the filtration of a signal. That is why the unique filters have been developed in their Laboratory.
Idea, design, research, listening
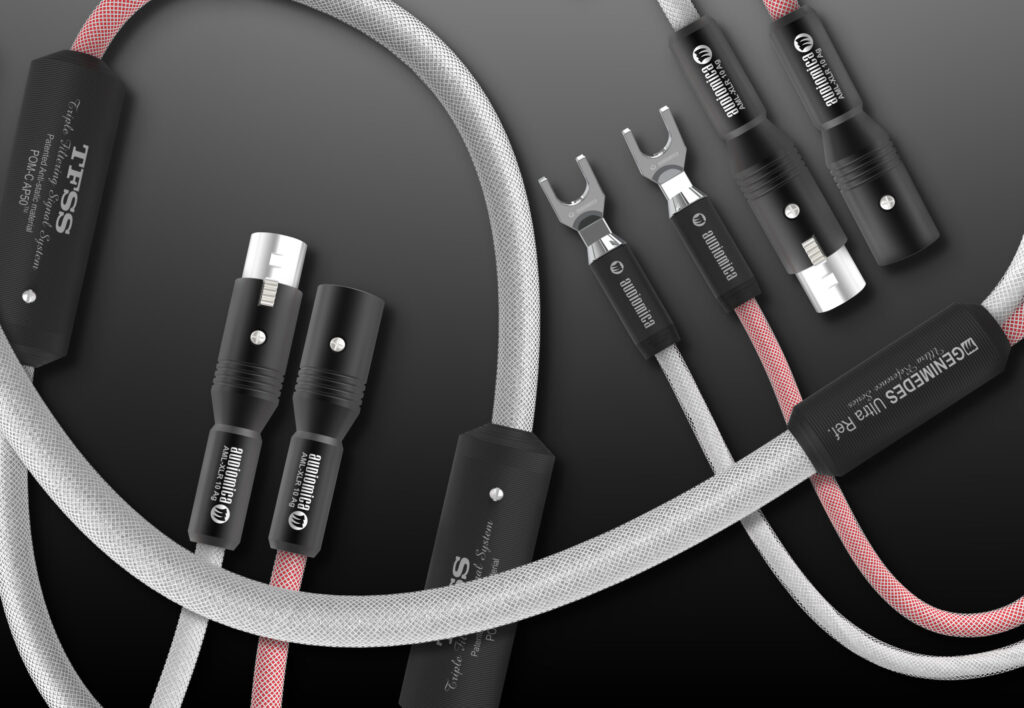
Every single process of creation begins with an idea. In this aspect we are receptive to suggestions of our workers, indirect clients and target consumers. It results in numerous innovative projects which very often evolve into totally new products or upgrades for already existing ones. Should you have any suggestions which you would like to share with them, please write tol: laboratory@audiomica.com.
Their long-standing experience in hi-fi cables manufacturing has taught them that there is always some space for improvement and doing something better. If there are people who suppose otherwise, they are certainly wrong. New technologies, brilliant notions, inventions… They keep their finger on the pulse.
A design phase is inextricably linked with research. They do most of the development research on their own. Moreover, they consistently extend their research base and incorporate new companies which closely cooperate with Audiomica Laboratory. The companies give them access to measuring equipment and newest technologies which are unobtainable for them.
Theory not always goes hand in hand with practice and thus after the laboratory research all the prototypes go to their listening room. In this room the final verification takes place. After this practical session, the prototypes go again through all the preproduction stages: idea, design, research and finally back to the listening room. Their analysis shows that only 20% of the prototypes successfully go through all the preproduction stages.
Despite the fact that they own plenty of listening equipment in a properly adopted acoustic room, they have also decided to lend the prototypes to a test group. They have practiced it since they introduced their Excellence Series. After they receive feedback from their test group, they implement all necessary changes and send the improved versions back for further evaluation. Tests carried out in over twenty different hi-fi systems resulted in an award from High Fidelity Magazine: Best Product 2012. The list of testers is not closed yet and we successively widen their number at each Warsaw Audio Show.
Conductors, raw materials
Audiomica Laboratory make their cables of silver and copper, as well as of alloys and electroplated variants of the aforementioned metals. The choice is dependent on many factors of which the most important ones are the kind and accuracy of a transmitted signal. Materials for a particular cable are chosen by trial and error which is obviously time consuming, but it is actually the only way to create a final product which will be able to match our expectations. The list of raw materials used by Audiomica Laboratory:
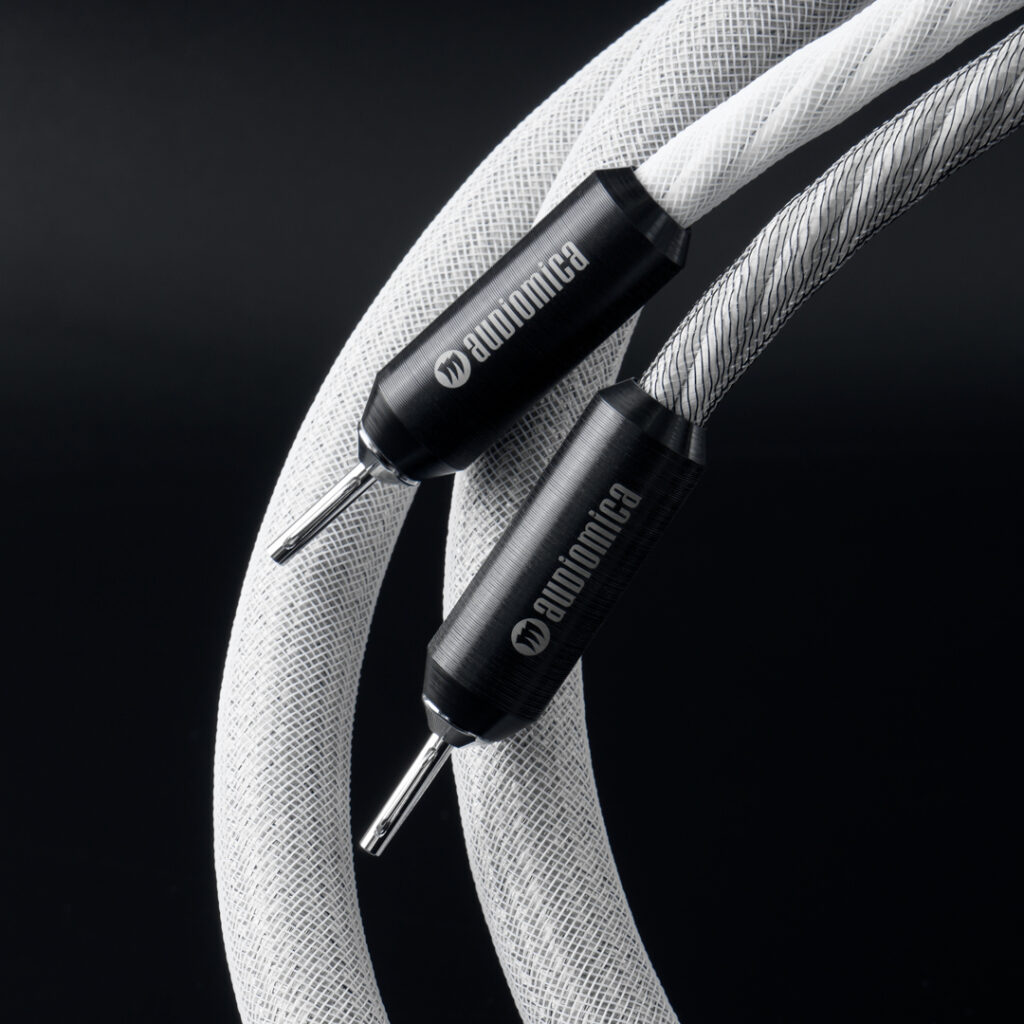
OCC-N6 and N7
Ohno Continuous Casting is the process of copper production whereby the number of crystals in a conductor is reduced. In OCC process the wire is slowly pulled out from melted metal. It allows to obtain copper of which single crystals are over 100 meters long. The copper produced in this way is also characterized by high purity.
The process was worked out by professor Ohno from Chiba Institute of Technology in Japan and patented in 1986. There are only a few companies which produce cables using this method. In OCC process the wire is pulled out more slowly that in conventional processes which consequently increases the cost of production. Copper produced in OCC process is considered to be the best type of conductor in respect of quality.
N6 and N7 stand for the purity of copper which amounts 99,9997 and 99,99997% respectively. Impurities constitute barely twenty/millionths. Due to really huge costs of OCC-N7 copper, we use it only in the top cables of Consequence Series while OCC-N6 goes with Excellence Series.
Silver-plated
OCC, OFC and LGC copper wires are put through our original process of electroplating called DCP (Double Coating Process). The process is extensively described below. Given the physical properties of the signal flow (the signal flows on the surface of a wire), we practically get a silver conductor with all the sound advantages of silver and copper.
Silver alloy
Silver-copper alloy is our original technology which is not developed anymore. Huge implementation costs exceed sonic values which constitute a priority at designing new structures. The alloy has been used to produce two wires which make a conductive wire in two structures: Mica and Borax. The biggest advantage of this alloy is transparency of the sound. The structures are dedicated to the systems which do not require interfering in the tone of the sound.
Silver-HG
Electrolytic silver known also as technical silver and registered by KGHM HG is obtained from electrolytic purification of copper or by Parkes method in which the metal is sorted out from lead ore which contains a dash of silver. The metal obtained in this way is marked by excellent mechanical and electric properties. All the undesirable additives of other elements which may appear in this electrolytic silver significantly contribute to a deterioration in the sound quality. That is why, it is important to determine the origin and composition of the metal and fortunately KGHM company guarantees such verifications. A multi-wire structure of the conductor was applied inter alia in Rhod Reference interconnect. Very good or even perfect sonic values of this metal encourage us to introduce it to our new products in the future.
CU-ETP
Melted cathode copper known also as electrolytic copper (ETP: Electro Tough-Pitch) is copper of which purity is at least 99.90%, electrical conduction not less than 101% IACS and oxygen content as low as 0,02 to 0,04%. It is used mainly in the electrical and electro-technical industry. CU-ETP copper is highly plastic and resilient, it is used only in power cords of Black, Gray and Red Series.
LGC (Long Grain Copper)
The fact that the wire is pulled out slowly enables to extend the length of copper grains and reduce their number to 210 in one meter. Thanks to the lower number of crystals, electrons encounter a lower number of transitions and impurities on their way, hence a smaller quantity of information is lost. This kind of copper is called functionally perfect copper. Long Grain Copper allows to achieve smoother and purer sound compared with cables using ordinary OFC copper. LGC copper has a few decimal places lower oxygen contain, less impurity and superior microcrystal structure which altogether result in much better quality of sound and picture. We currently use this conductor in our HDMI cables.
OFC vs. OFHC
OFC is oxygen-free copper of high purity. The version used by Audiomica Laboratory is OFHC (Oxygen Free High Conductivity) N4 and N6 which has a lower level of impurity. This type of oxygen-free copper of high conductivity is ahead of OFC in terms of quality. Sonic differences in relation to OFC include more precise bass, larger isolation of instruments, better space expression and more distinct sound in high frequency sounds. This material is most frequently applied in Black and Gray Series.
Dielectrics and insulation
Each insulating material adhering to a conductor is actually only a part of an imperfect system. Cable insulation as well as printed circuit materials absorb energy which is partially lost in the conductor. The rest of this energy is kept and then released as distortions. Each type of insulation has different properties. It is obvious that air would be the best insulator but air insulation technology is unobtainable for the time being. The best dielectric in practice is Teflon and its variations. Teflon is very tough, light and resistant to high temperature, humidity and oxidization. Audiomica Laboratory uses both Teflon and its variations in the cables we produce. The properties of these dielectrics can be improved by letting gas or air bubbles inside (extruding). Through this process the material is filled with thousands of bubbles and in practice the conductor is to large extent surrounded by the air. The dielectrics are used not only to influence the quality of the sound through their dielectric properties but also because of the fact that each type of insulation may have an impact on the characteristics of the sound. In order to achieve the best possible result from each cable, it is important to match a certain cable to proper insulation. If we use extruded polythene, it will get quite the same measurable properties as Teflon but the sound will be different. Many other companies manufacturing cables use traditional insulators e.g. PVC. It is the cheapest and rather not good option. PVC used e.g. in interconnects has too large distortions to be applied in high quality cables. Audiomica Laboratory do not use PVC in the role of dielectric but only as an exterior layer which is insulated from the conductor by means of the aforementioned dielectric and a few other layers e.g. foil screens or multi-wire braids. PVC used as an outer coat provides flexibility of the whole structure which makes adapting the cable to a system easier. What is more, extruded PVC guarantees also some additional and highly desirable anti-vibration properties.
Audiomica Laboratory in 99% cases use extruded Teflon as an insulator. It is called FEP (fluorinated ethylene propylene). The choice was obvious as it is the best insulator so far.
FEP material was invented and patented by Dupon company in 1960. It is a copolymer of fluorinated ethylene known also as TPFE (Teflon) invented as early as in 1938. So FEP is a modern version of Teflon. This polymer is characterized by high stiffness and resistance to tearing which make it especially useful for insulating cables and wires. It keeps its resistance and stiffness in high temperatures. It is also corrosion-proof and resistant to bending. The other excellent properties are: chemical resistance to all kinds of chemical substances, dielectric properties and low fraction coefficient. FEP material is chemically neutral.
Extruded Teflon comes into existence as a result of letting countless air bubbles inside and it is done due to the fact that the air is even better an insulator than Teflon alone. The only better one is a vacuum.
Plugs and solders
Our plugs are precisely plated with gold, silver or rhodium through the DCP electroplating process which one may find described above. The plugs are firmly connected to the cable with the best possible solder. Thanks to the choice of right flux and metallurgy process, soldering has been optimized in terms of joints smoothness which are now deprived of any deformations.
All the solder joints, including even silver solders, are poor conductors. There are some audible differences between different solders and they result from the quality of joints. Audiomica Laboratory soldering process does not use much silver because the more silver in solder, the more difficult it is to join two materials. Right proportions of main components and many other important details explain how it is possible that even as inexpensive cable as Beryl Gold can sound that good.
All the materials are painstakingly chosen in the process of a meticulous selection. The selection is based on electric correctness research, material purity research and sonic values.
Z-type BFA banana is a high quality banana plug with BFA ending made of copper-beryl alloy and plated with 24-carat gold or silver in the process of DCP electroplating. Z-type means in-length cut of a pin which results in perfect adherence of the whole surface of the plug to the socket. It is an uncompromising solution as the plug adhering to the socket with the whole surface does not increase electrical resistance. Signal flows with no interference. The precision of workmanship and the materials used for production assure crystal clear and interference free sound.
RCA and XLR plugs are most well known and widespread of all. They are usually made of copper or copper- beryl alloy. To increase mechanical and sonic values, Audiomica Laboratory plugs and pins are subject to a DCP process. The surface which is obtained in this way: gold-, silver- or rhodium-plated, protects copper from oxidation. Copper alone is soft which may cause the plug to widen to such extent that it will not fit the socket. The loss in mechanical property of the plugs is connected with the increase of resistance which translates into sound value losses.
Audiomica Laboratory uses many different plugs for most diverse connections. Rules of selection, the way of electroplating and kind of solder are the same. The aim is one and unchanging, to ensure lossless signal flow from the beginning to the end.
We use our original plugs in Black, Gray and Red Series. In higher lines: Excellence, Ultra Reference and our top line, Consequence, we use original or slightly modified WBT plugs.
Directionality and burn-in
There is this theory according to which a cable plugged in one direction should perform better than the same cable plugged in the opposite direction. The theory is called directionality. Our long experience in cable manufacturing does not allow us to explicitly declare directionality of a given structure. Even though listening tests lead to the conclusion which supports the theory of directionality, this theory seems to be invalidated by experience. Many times our recommendations on how to plug a certain cable proved wrong in the client’s system. The influence of certain electronics and speakers is not always predictable and there is an infinite number of configurations to boot. The best way to choose the direction of a given cable is to plug it both ways and then select the option which suits you best.
The only cables which make an exception are cables with filters. But even here the rule may not always be valid and it is more a recommendation rather than a stiff principle. The filters are placed asymmetrically on cables i.e. the filter is closer to the plug on one side. We recommend to use this side to plug a source of the sound in case of connection cables and to plug loudspeakers in case of speaker wires. But still these are only recommendations, not rules.
All new cables which are plugged to an audio-video system require so called burn-in process. It is very easy to state a difference between a new cable and the one which has played for 100 hours. New cables play brightly and bass sounds mechanical. Burn-in arranges the sound and makes it more flexible, in other words it defines the sound. It is difficult though to determine how long the process should last. The time needed for burning cables and improving the sound they carry depends on the structure of a cable and material used for its production. The biggest changes may be noticed at silver-plated cables with Teflon insulation. The burn-in time is also dependent on the system we use and the kind of music we listen to, plus how long we listen to music during the day. This time may differ and it ranges from 3 weeks to 3 months.
It is not without reason that we describe the two phenomena of directionality and burn-in together. After defining directionality of a certain cable in our system, the burn-in process starts. When the cable is already burnt and optimal sound is achieved, the cable should not be plugged the other way. There are no electric contradictions, however, the sound will lose the quality.
Anti-interference filters: DFSS, PFSS and TFCT
Designed by Audiomica Laboratory, the anti-interference filters function as a complement to the whole cable structure. Contrary to this popular belief, filters do not muffle and slow down the sound. We have put a lot of work and effort so that their influence can be both subtle and effective. The most important thing is that by means of the filters we are able to correct some current parameters which are considerably responsible for the final sound. A certain sound is the final destination and thanks to our filters we are capable of controlling it. More information on the structure of the filters may be found in FILTERS bookmark
Double Coating Process (DCP)
Double Coating ProcessTM is a technology of applying an electroplated coating. The technology was invented and patented by Audiomica Laboratory. 90% of plugs and sockets existing on the market are notorious for their poor quality coating. Gold-, rhodium- and silver-plating processes which are normally on offer leave a lot to be desired while the quality and thickness of the plating are of great importance. It is not yet another audiophile whim – it’s physics. Only the current of low frequency or the constant one flow through the whole section of a conductor and even such currents must be eventually released. In other cases the current does not get to the inside of a conductor but flows on the surface. That is why the quality of the surface of a conductor and a plug is so significant.
DCPTM product is a homogeneous coating which is 2 to 20 microns thick. European standards are 3 microns of electroplated surface while Chinese standards are 1-2 microns. As the name itself indicates, the coating is applied twice. After the initial electroplating, the surface is cleaned, measured and sent to the second electroplating. The whole process is laborious and expensive but it gives us every confidence that the surface acquired in this way will be perfect. Electric and mechanical parameters are incomparably better than in case of standard processes of applying electroplated coatings.
CTB screening process
Contrary Twisted BraidsTM is the name of the technology of applying screens with contrary twisted braids. The process was entirely invented and patented by Audiomica Laboratory. Conductor screening is not always necessary but if it is, it must be done perfectly well. Otherwise the only thing we get, is a superfluous ballast which badly influences the flexibility of the cable and makes it much harder to apply it to the audio-video equipment. Our cables of higher series have better screening. It results from a practical reason that they are used in systems of higher complexity where the influence of a negative electromagnetic field is more intensive.
At the beginning we developed DSSTM – Double Screen SystemTM. It is a combination of double screening and a special braid of conductive wires. The multi-wire braid eradicates the mutual induction of currents and thus eliminates interference. It is done by means of the magnetic field which is produced by the neighbouring wires. The system is successfully used even today in the cables of Black, Gray and Red Series.
The CTBTM system has been designed for more advanced cables. In this case screens are selected for each cable individually. The process is very persistent as it involves numerous measurements and tests which unambiguously show the advantage of this technology over the traditional method of screening. In CTBTM system the screens are applied with contrary twisted multi-wire braids. The thickness of each braid wire, their number and way of combining the layers of the braids is a parameter patented by Audiomica Laboratory. The impact of an electromagnetic field on a cable equipped with CTBTM system is zero or close to zero depending on the configuration of the abovementioned variables.
Mica Security Liquid
HISTORY
We have been trying to improve a separating substance for over five years. There are a lot of materials, liquids abd substances for similar purposes. However, they do not meet certain requirements. All of them are difficult to remove and, what is more, they are very often either too thin (polyurethane and epoxy resins) or too thick (silicone and latex) before drying. It is so because these materials are designed to perform certain tasks and so far, a substance filling plug cases has not been developed. Nevertheless, our cooperation with a leading manufacturer of resins, acrylics and latex resulted in our original project called Mica Security Liquid (MSL).
This fluid applied as a space filler covering plug solderings has already been used for a couple of years. A similar separating substance was used for our HDMI plugs and now we are introducing the latest version of this filler. It is not without reason that this project coincides with the upgrade of our top cables – Consequence Series. RCA-WBT plugs which go with interconnects of this series have been filled with Mica Security Clear.
PROPERTIES
– The liquid has excellent anti-vibration properties. Thanks to its extremely liquid consistency it fills all the micro slits protecting the whole soldering surface.
– MSL after hardening shows huge mechanical resistance and high thermal and chemical resistance. It is also waterproof.
– It removes heat emitted by current and thus extends the lifespan of soldering.
– Electrically neutral and non-flammable.
– Hard-flexible, easily removable with UVA light of 300-400nm wavelength. Especially useful property when someone needs to replace plugs.The main task of Mica Security Liquid is protecting solderings mechincally: transport, weather conditions, accidental falls, etc. As the material is electrically neutral, it does not affect the quality of transmitted signals. It does not upgrade and downgrade the sound. In the nearest future, we plan to use this material not only in our plugs but also in TFCT anti-interference filters.
PARAMETERS
– the solids content – 60-65%
– pH 9.5
– the ammonia content – about 0.45 ppm
– hardening – 5h/40oC
By-name quality confirmation. Certification
To assure the highest quality control right from the start of our activity we introduced a by-name quality confirmation. It is obvious that the responsibility for the quality of a final product lies with the whole team including not only an originator, designers and engineers but also a quality inspector. Audiomica Laboratory cables are hand assembled and manufactured on a small scale. Our certificate bears personal signatures of a person who assembled the whole structure and a person who carried out the final test verifying the electromechanical correctness. The certificate also carries the unique serial and batch numbers which tell the exact date of production and materials used for creating a given cable. It allows fast identification of the authenticity of Audiomica Laboratory products
Series, purpose and nomenclature
Audiomica Laboratory boasts six lines of cables designed for audio-video purposes, ranging from low-end through hi-fi to high-end. On our website in the bottom left hand navigation panel one may find a list of all our series beginning with the most advanced and most expensive one, Consequence Series, to professional cables of Black Series placed at the bottom.
The series in order of prestige (starting with the most advanced):
-Consequence Series
-Ultra Reference Series
-Excellence Series
-Red Series (Reference)
-Gray Series (Transparent)
-Black Series (Gold)
The name of our company and the names of most of our cables derive from minerals. Each name was adjusted heeding unique characteristics of a given mineral and each mineral may be easily associated with a certain cable through its colour, shape and properties. However, Ultra Reference Series is an exception. The cables of this series bear names of the largest moons in our galaxy. We strive to make each our series of cables complete. It means that we want each individual series to contain cables of one sound characteristics which the listener will use to plug the whole audio system with. Why series? It was our assumption right from the start to create a complete set of cables for the whole system so that our clients do not need to wonder if interconnect “x” will work well with speaker cable “y” and power cord “z”. The cables of each series are painstakingly chosen in terms of electric and sound parameters. We will explain it with the use of Red Series (Reference):
Dolomit speaker cable made of copper which carries warm and natural timbre + Quan jumpers for bi-wiring made of silver-plated copper and carrying more analytical sound + silver Rhod interconnect which is ultra accurate and precise + Jasper power cord made of electrolytic copper, free of distortion and full of dynamics = a perfect and complete composition which constitutes a well thought out track for the sound.
Nevertheless, it does not mean that the cables of different series should not be mixed together. It is even an interesting experience which, however, involves trial and error method to find the proper sound. Whereas when you choose the cables of one series you can be sure of the final result.
This well designed structure of the conductors guarantees satisfaction for years without the slightest need to change anything. This is the aim of our mission.
There is a lot more insight and information on the philosophy and design techniques on the Audiomica website, click on the logo above to visit or call us for more information.
Thanks for turning me onto the Audiomica labs cables, they truly are the most natural sounding cables I’ve heard. My listening sessions have now doubled because of these cables.
Thank you,
Joshua
These cables have been a revelation! Natural, fast, deep bass what more can you ask, it’s like not listening to cables anymore.
Just wonderful.
WOW! What fantastic cables at prices that are affordable and the average audiophile can buy without breaking the bank
Absolutely amazing cables! The Consequence power cable is just too good for the money! Energy, musicality, pace, just sounds right. Thank you Steve so much for your help and turning me onto this cable line. Excellent customer service and excellent products, home run!